Votre plan d’entrepôt est-il à jour ? Recevez un plan en 2 semaines.
Driving Warehouse Efficiency: Exploring Effective Supply Chain Management Methodologies
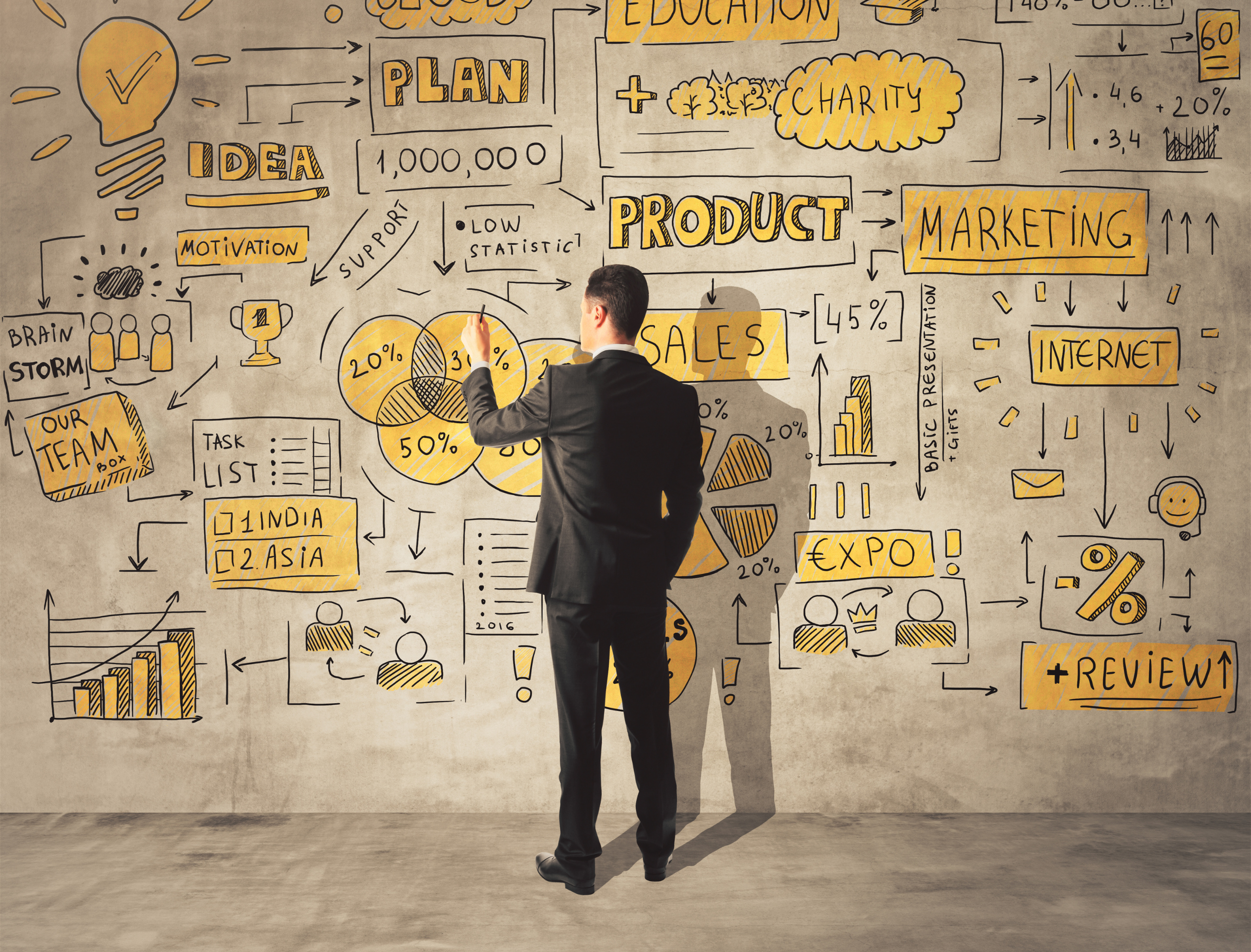
By Chris Hagle
November 15th | 3 min read
Exploring the Power of the 5S Principle in Supply Chain Management
Productivity is a term that is often misunderstood and overused. With numerous measures and techniques available, leaders may find it challenging to proactively tackle productivity issues. However, an easy first step is focusing time and attention on what matters to your organization.
It may seem like an obvious way to increase productivity, but obvious doesn’t always mean it’s easy.
In our latest #PalletsofWisdom blog post, Chris Hagle delves into this topic, offering insights on how a simple methodology such as the ‘5S Principles’ can help drive productivity and ensure time is spent on value-add activities.
Methodology to Prioritize Value-Add Tasks
The 5S principle goes beyond simply having items in an identified and labeled place. It is a framework that is imperative for driving a culture of continuous improvement within your organization. Starting with leadership buy-in, all employees within the organization must embrace 5S to ensure its success. Implementing 5S as part of your operations will yield many benefits, which are explained below:
What is 5S in Supply Chain Management?
Sort – Eliminate whatever is not needed by separating needed tools, parts, and instructions from unneeded materials.
Set in Order – Organize whatever remains by neatly arranging and identifying parts and tools for ease of use and accessibility.
Shine – Clean the work area from top to bottom, take pride in a clean environment.
Standardize – Schedule regular cleaning and maintenance by conducting Sort, Set in Order, and Shine daily.
Sustain – Make 5S a way of life by forming the habit of always following the first four S’s.
This response is frequently encountered during site visits. Unfortunately, by not tracking employee performance, you are actively reducing accountability within your organization. It becomes challenging to have factual conversations with employees without sufficient data to support observations. Implementing a labor management tool allows you to recognize high performers (potentially with incentive pay) and provide coaching to underperformers. This ultimately boosts company performance and fosters a culture of continuous improvement.
Benefits of Implementing 5S for Supply Chain Management
Implementing 5S can bring numerous benefits and improvements to your organization and operations, including:
- Improved Safety: With 5S, you’ll experience fewer slips, trips, and falls as an organized workspace reduces hazards.
- Higher Equipment Availability: Easily identify when something is missing or not placed where it should be, ensuring that necessary tools are always accessible.
- Lower Defect Rates: Having the right tools for the job eliminates the need for workarounds with other tools, leading to higher quality outputs.
- Reduced Costs: Spend less time searching for things and more time on value-added activities, optimizing resource utilization.
- Increased Production Agility and Flexibility: Knowing what you have available allows you to swiftly shift operations to meet customer requests.
- Improved Employee Morale: Working in a clean environment where things are easy to find and use boosts employee satisfaction and productivity.
- Better Asset Utilization: By keeping things organized, you avoid buying duplicate items and only replace them once they wear out, reducing needless spending.
- Enhanced Enterprise Image: Impress your customers, suppliers, employees, and management by showcasing an organized and efficient workplace.
To summarize, embracing the 5S methodology in supply chain management can bring about transformative changes within an organization. By promoting organization, cleanliness, and standardization, businesses can drive efficiency, improve quality, reduce costs, and create a culture of continuous improvement. Implementing the 5S methodology is not a one-time activity but rather an ongoing journey towards operational excellence.
Ready to take your operations to the next level? Connect with a supply chain expert to learn how you can maximize productivity in your workplace.