Is your Warehouse Layout Up to Date? Receive an Updated Layout in 2 Weeks.
Every Facility Should have an Up-to-date Warehouse Layout
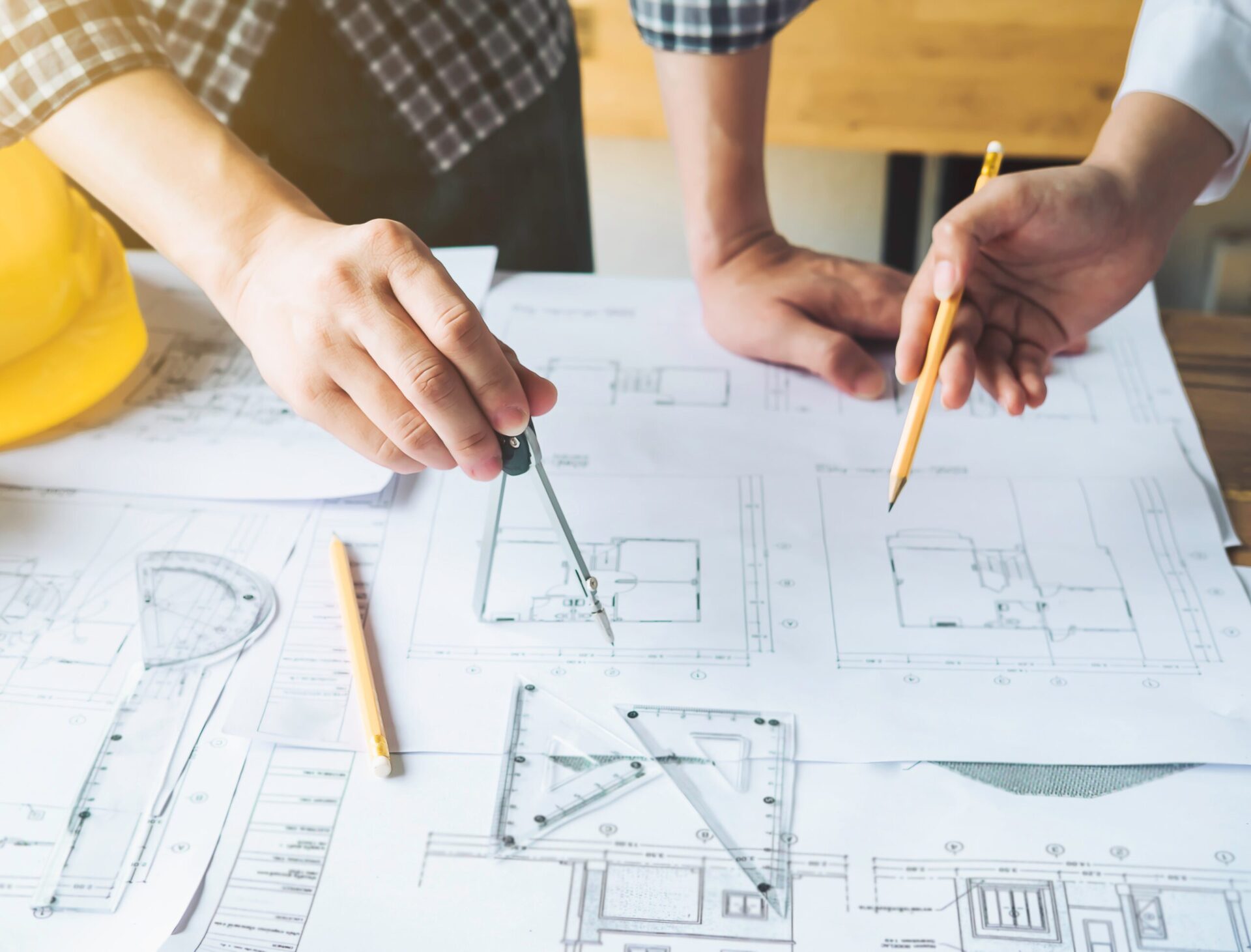
By Steve Zerter
May, 2017 | 4 min read
Distribution Center Design
When we start a project, we’re never surprised to find out that the client doesn’t have up-to-date or complete plans of their warehouse. Very few operators have up-to-date warehouse layouts, almost none have all the useful information that can be included on these drawings. Some may have a decent floor plan but rarely do they have building or rack elevation drawings. A significant group don’t even have a rough sketch and perhaps can only guess at the clear height or heights of the building.
A partial list of the information that we collect follows, additional information is collected as required.
- Rack and aisle layout, including all rack dimensions (upright center to center, rack depth, spacer length, etc.) All types of storage equipment will be included
- All aisle widths and rack to wall clearances
- Rack elevation profile coding, including floor to top of load beam dimensions for all racks
- Number of pick slots, including hand-stack and flow-rack slots
- Rack / aisle numbering and details of the numbering system
- Conveyor layout (within reason)
- All pertinent building dimensions, column sizes, column spacing, clear heights
- Location of obstructions that affect storage (down spouts, sprinkler risers, air units etc.)
- Dock and personnel door size and location
- Cooler / Freezer door size and location
Our physical audit process is simple enough. Most of the work is done with a common measuring tape, and a handheld laser device. There is a lot of leg and arm work involved – a very large facility can take a few days. Larger facilities with regular racks laid out in consistent patterns may present less of a challenge than smaller buildings with assortments of equipment that were bought at random over the years. The experience of having performed numerous audits makes what might seem like a huge task, doable and safe, with no disruption to operations.
Once the warehouse layout is done and recorded in AutoCAD we have a clear and accurate starting point. We can then calculate the existing cubic storage capacity, come up with viable improvement options and compare them to the existing situation. Budget pricing for reset or expansion options can be developed. The time spent on site allows us to become familiar with the facility and greatly reduces the possibility of errors that can be the result of incorrect or missing information.
To supplement your reading on how to create and optimize warehouse layout design, check out our whitepaper about Product Slotting.
Reach out to the LIDD team to learn more about distribution center design and optimizing your warehouse operations.