Is your Warehouse Layout Up to Date? Receive an Updated Layout in 2 Weeks.
Infrastructure: Supply Chain’s Missing Link
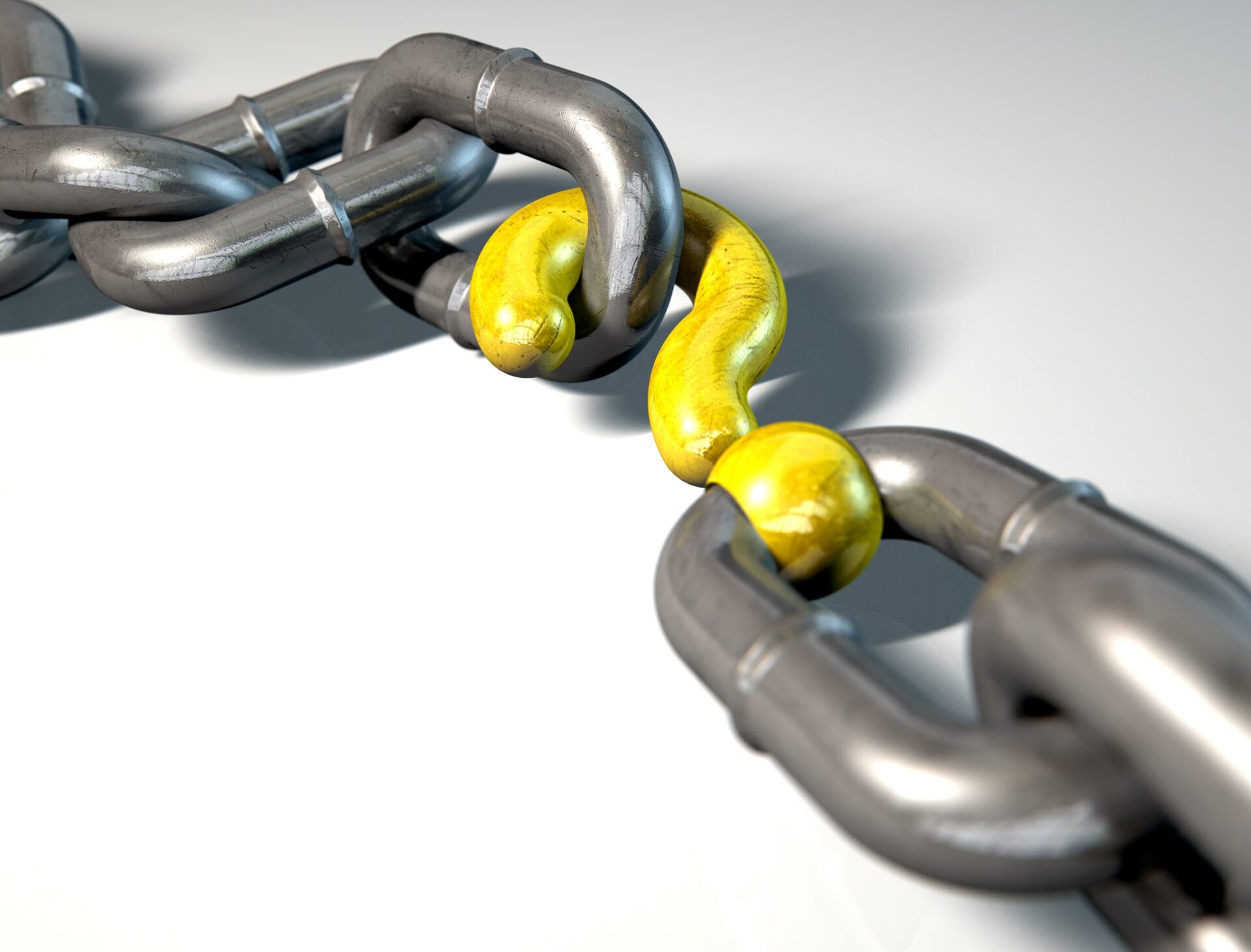
By Charles Fallon
March 11, 2014| 2 min read
At LIDD, we’ve decided to make some effort to put “supply chain infrastructure” on the map.
If you google the term “supply chain”, you’ll find dozens of definitions that say the same thing: the supply chain is the flow and transformation of goods from raw materials in the hands of producers to finished goods in the hands of consumers. What’s missing from these definitions is the recognition that supply chains are more than just a series of activities: they are a set of physical assets in which these activities take place.
These physical assets are the buildings in which we manufacture and distribute things; they are the materials handling and processing equipment used in those buildings; they are the transportation equipment used to move product from one location to another; and, they are the information systems used to direct and execute the supply chain. Together, they form a company’s supply chain infrastructure.
Most companies don’t see these assets as a single, cohesive infrastructure. Instead, different departments control different parts – systems belong to IT while facilities and transportation are the purview of operations. And within operations, manufacturing, warehousing and transportation are split between various VPs. Running complex supply chains with armies of people executing thousands of transactions each day makes this “divide & conquer” organizational strategy sensible. But that’s no way to design and build an efficient supply chain.
Think about the various department-level budgets your company produces each year; consider all the requests for capital expenditures. Imagine if you consolidated all those capital expenditures under the single heading of “supply chain infrastructure” – requests for new fork trucks, new trailers, building modifications, new scan guns, a systems upgrade, etc. If they were on a single page, would they add up to a single cohesive plan? Or would it look like a hodgepodge of mini-solutions to smaller problems that make no reference to the larger goal?
My guess is it would look more often like a hodgepodge than a synchronized master plan.
Reach out to the LIDD team to learn more about warehouse slotting and optimizing your warehouse operations.
Supply Chain Strategy Consulting