Is your Warehouse Layout Up to Date? Receive an Updated Layout in 2 Weeks.
Simplifying Inventory Management with Cross Docking
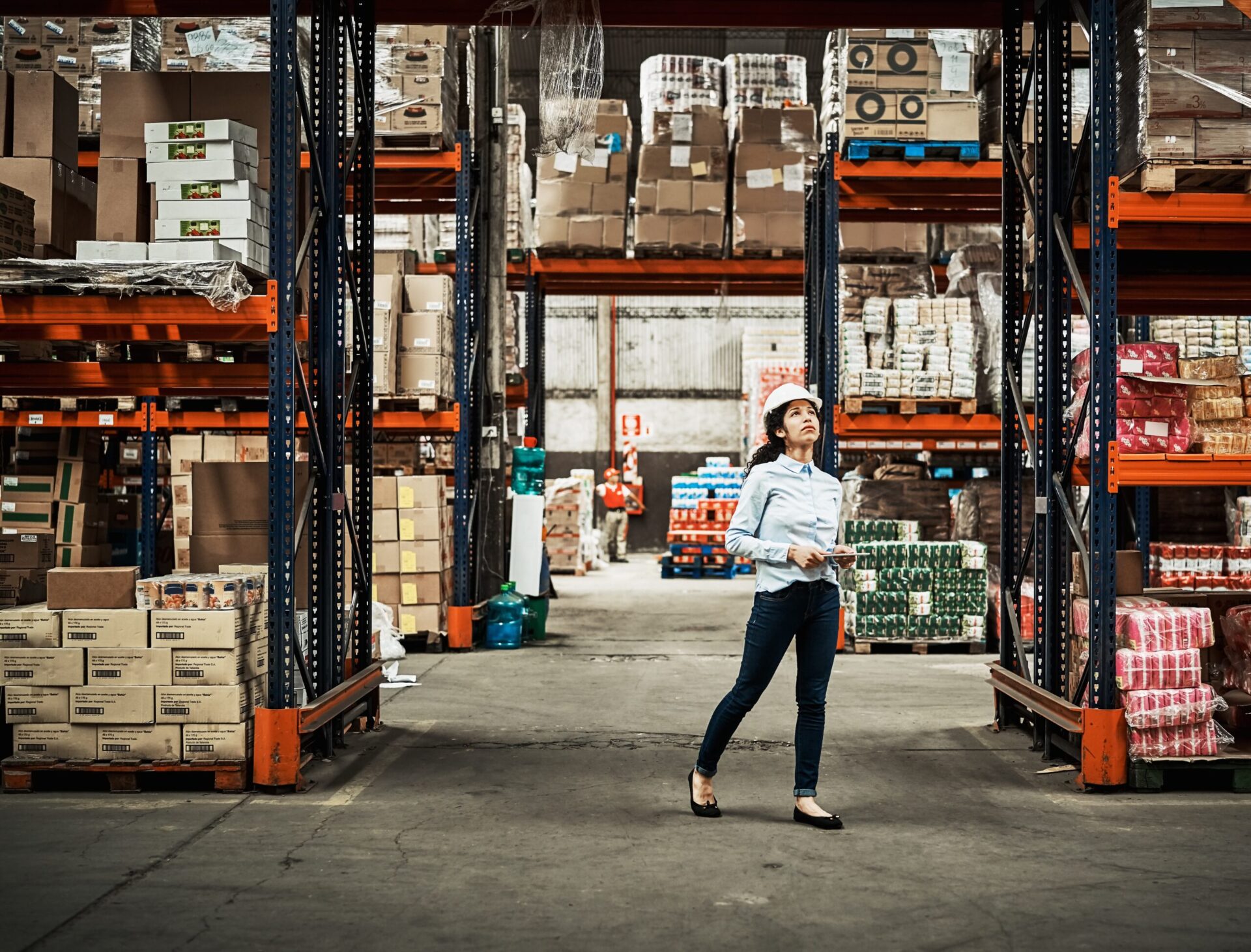
Boost Operational Efficiency with Minimal Handling and Storage
Author: Alexa Forsyth
March 26, 2025 | 3 min read
Finding the optimal way to store inventory can be a complex puzzle as it depends on the nature of the items in the warehouse. Are the items oversized? Can they fit into specific slots? Should similar items be grouped together? How quickly do they sell, and do they have high seasonality? Should they be stored in one centralized location or distributed throughout the warehouse? Many factors come into play when determining the best storage strategy for each item.
But it doesn’t end there. Once you’ve determined the best storage locations, you still need to figure out how to efficiently put the inventory away and pick it when needed. It’s the accumulation of these small decisions that can make or break warehouse efficiency.
But what if we could just skip all that hassle?
What is Cross Docking?
Cross docking revolutionizes the traditional warehousing process by bypassing the storage, picking, and putaway phases. Instead of adhering to the conventional sequence of Receiving > Putaway > Picking > Packing > Shipping, cross docking simplifies the process to Receiving > Shipping, eliminating and minimizing unnecessary handling and storage time. This method ensures the swift transfer of goods directly from inbound vehicles to outbound vehicles, optimizing efficiency and reducing operational complexities.
Which Industries Benefit from Cross Docking?
Emerging in the 1930s to bolster efficiency within the trucking industry, cross docking evolved into a fundamental practice for both Less Than Truckload (LTL) and Full Truckload (FTL) shipping. This warehouse process finds its ideal application in Business-to-Business (B2B) industries, as large shipments are incoming and outgoing of the distribution center. Conversely, its applicability in Business-to-Consumer (B2C) sectors is limited due to the complexity involved in processing shipments destined for numerous final destinations and the meticulous sorting of inventory that would require at a granular level.
Industries characterized by high product seasonality can particularly benefit from cross docking practices. For instance, a clothing retailer anticipating the arrival of a holiday collection from overseas can swiftly divide the shipment into pallets destined for separate stores upon receipt at the warehouse. This enables stores to promptly adapt to evolving fashion trends and minimize inventory markdowns.
Cross docking holds significant relevance in grocery retail as well, where perishable goods require rapid delivery from vendors to multiple store locations. By ensuring timely delivery and quick turnaround times, cross docking preserves the freshness and quality of inventory, thereby meeting the stringent demands of grocery retail.
Benefits of Cross Docking
Cross docking offers many advantages, with one of the most significant being the elimination of the need for long-term storage of goods. This elimination, or substantial reduction, of storage requirements yields numerous benefits across various facets of warehouse operations:
- Streamlined Warehouse Design
The need for extensive warehouse infrastructure, such as racking and storage space, is significantly diminished. With fewer items stored long-term, the physical footprint of the warehouse can be minimized, allowing for a more efficient layout and utilization of space. - Mitigated Inventory Aging and Expiry
Since cross docking prioritizes the immediate movement of goods to their final destination, there is less opportunity for items to become obsolete or outdated while waiting in storage. This enables warehouses to swiftly adapt to changes in market conditions and customer preferences. Furthermore, the likelihood of inventory expiry is greatly reduced, as goods are not kept in storage for prolonged periods. - Simplified Training Processes
The elimination of traditional picking and putaway procedures streamlines the training process for warehouse personnel. Employees can quickly ramp up their skills and productivity, as they are not required to master more complex warehouse operations. Additionally, with certain warehouse tasks eliminated, the overall workforce requirement is reduced, reducing labor costs for the warehouse.
Limitations of Cross Docking
While cross docking can provide substantial benefits in terms of supply chain efficiency and responsiveness, it’s crucial for businesses to conduct thorough assessments of potential drawbacks and determine whether cross docking aligns with their operational requirements.
- Inability to Further Treat Goods
A key drawback of cross docking is the lack of capability to perform any further processing on the goods. Items that need packaging or wrapping cannot be accommodated within this system. - Dock Congestion
Another limitation arises when items arrive in multiple inbound shipments, requiring the staging of the initial shipment until subsequent inbound shipments arrive. This can lead to congestion and disorganization on the receiving dock. Insufficient planning or capacity may exacerbate this issue, creating bottlenecks and resulting in delays and inefficiencies in the cross docking process. - Dependency on Transportation Networks
Finally, cross docking relies heavily on reliable transportation networks to ensure the timely delivery of goods between distribution centers, suppliers, and customers. Delays or disruptions in transportation can disrupt cross docking operations and impact overall supply chain efficiency. Companies with their own fleet of dependable transportation vehicles may mitigate this risk to some extent.
The Bottom Line
Cross docking is a powerful tool for improving supply chain efficiency and responsiveness, especially in industries with high-volume, fast-moving goods. By understanding its principles, applications, benefits, and limitations, businesses can leverage tool to navigate the complexities of modern warehousing and logistics.
Looking for guidance on your distribution strategy? Connect with Alexa Forsyth to explore how LIDD can help.
For more updates, follow us on LinkedIn.
Related Posts
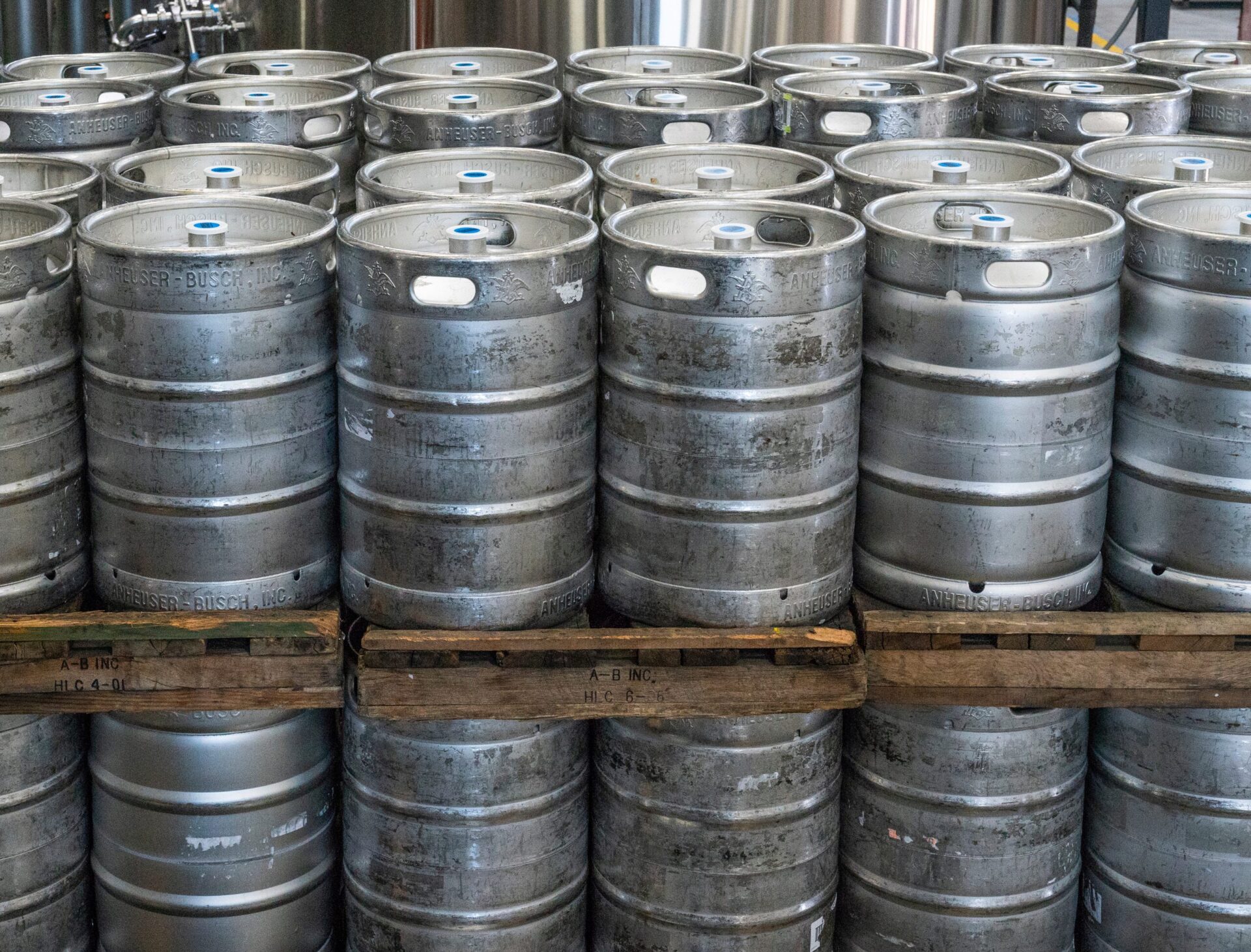
Bulk Storage: Are you using it efficiently?
Learn how to optimize your warehouse layout storage for maximum efficiency. Discover strategies to improve bulk storage utilization and overall warehouse capacity with LIDD’s expert insights.
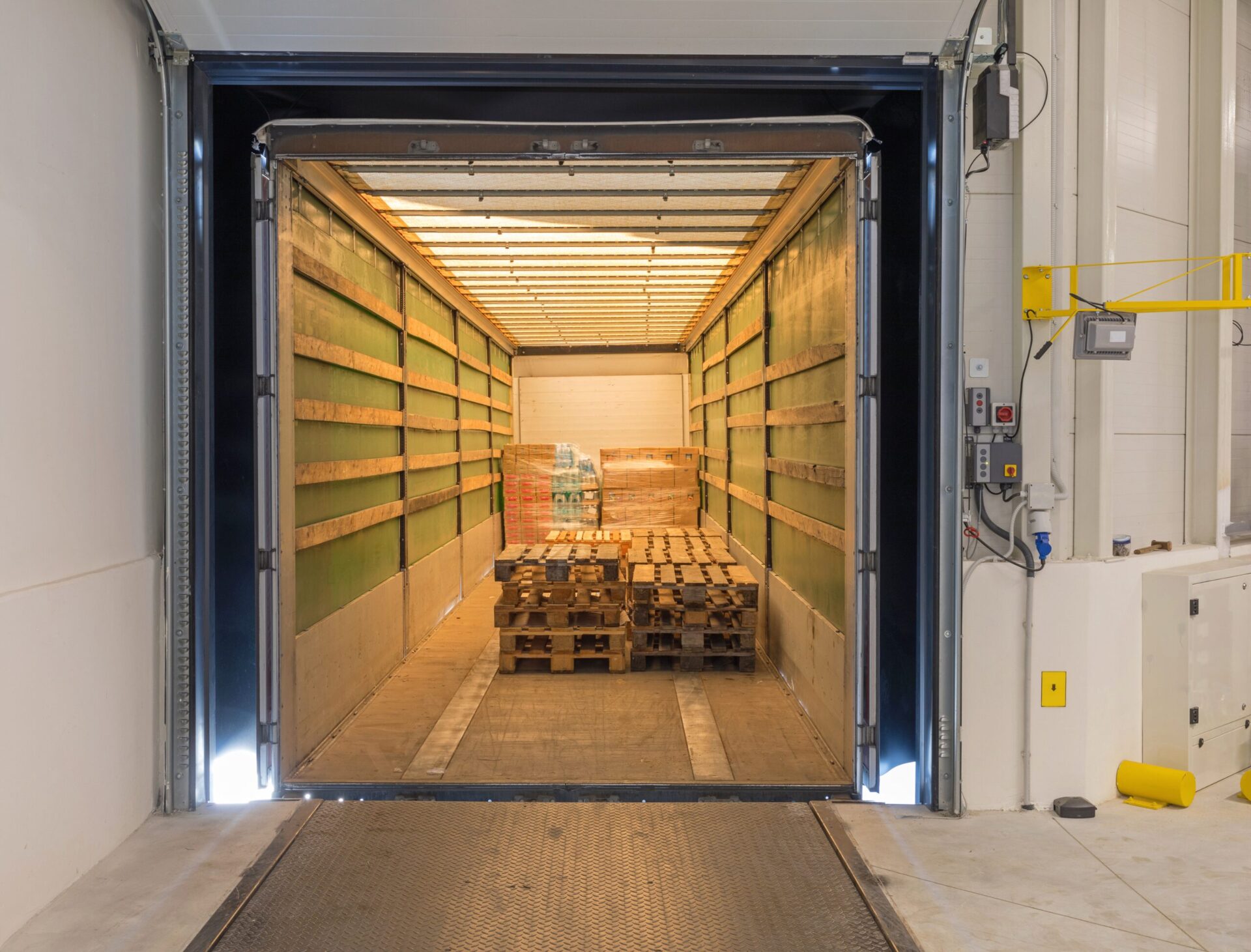
A Guide to Warehouse Dock Equipment
This guide dives into the types of warehouse docks, how they cater to specific needs, and why selecting the right dock is vital for a distribution center’s efficiency.
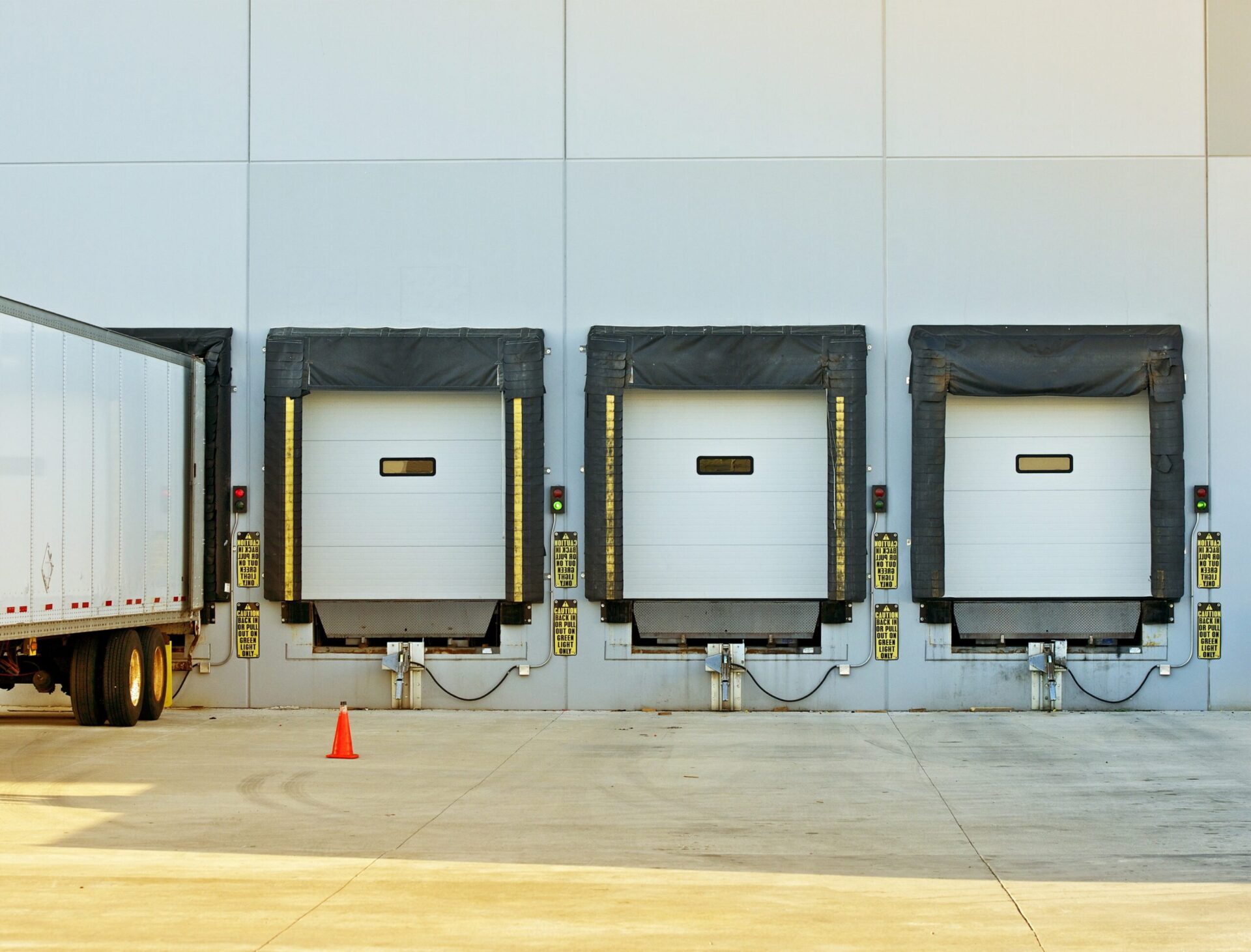
A Guide to Warehouse Docking Design
This guide dives into the types of warehouse docks, how they cater to specific needs, and why selecting the right dock is vital for a distribution center’s efficiency.
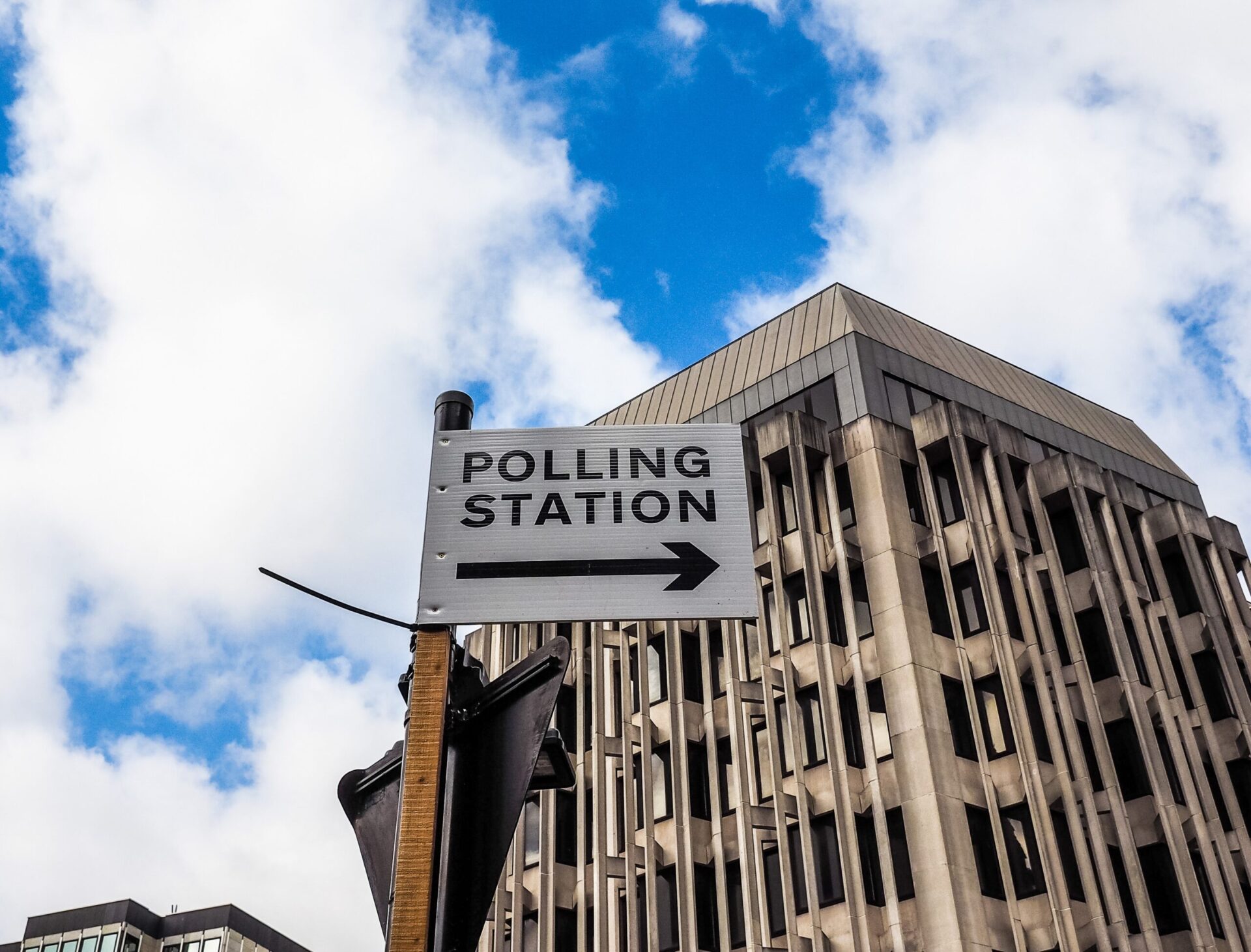
A Warehouse Is Like a Polling Place
By Gabrielle Tiven November 29, 2016 | 2 min read This election season I had a strategy for voting….