Is your Warehouse Layout Up to Date? Receive an Updated Layout in 2 Weeks.
The Vicious Circle of Picker Congestion
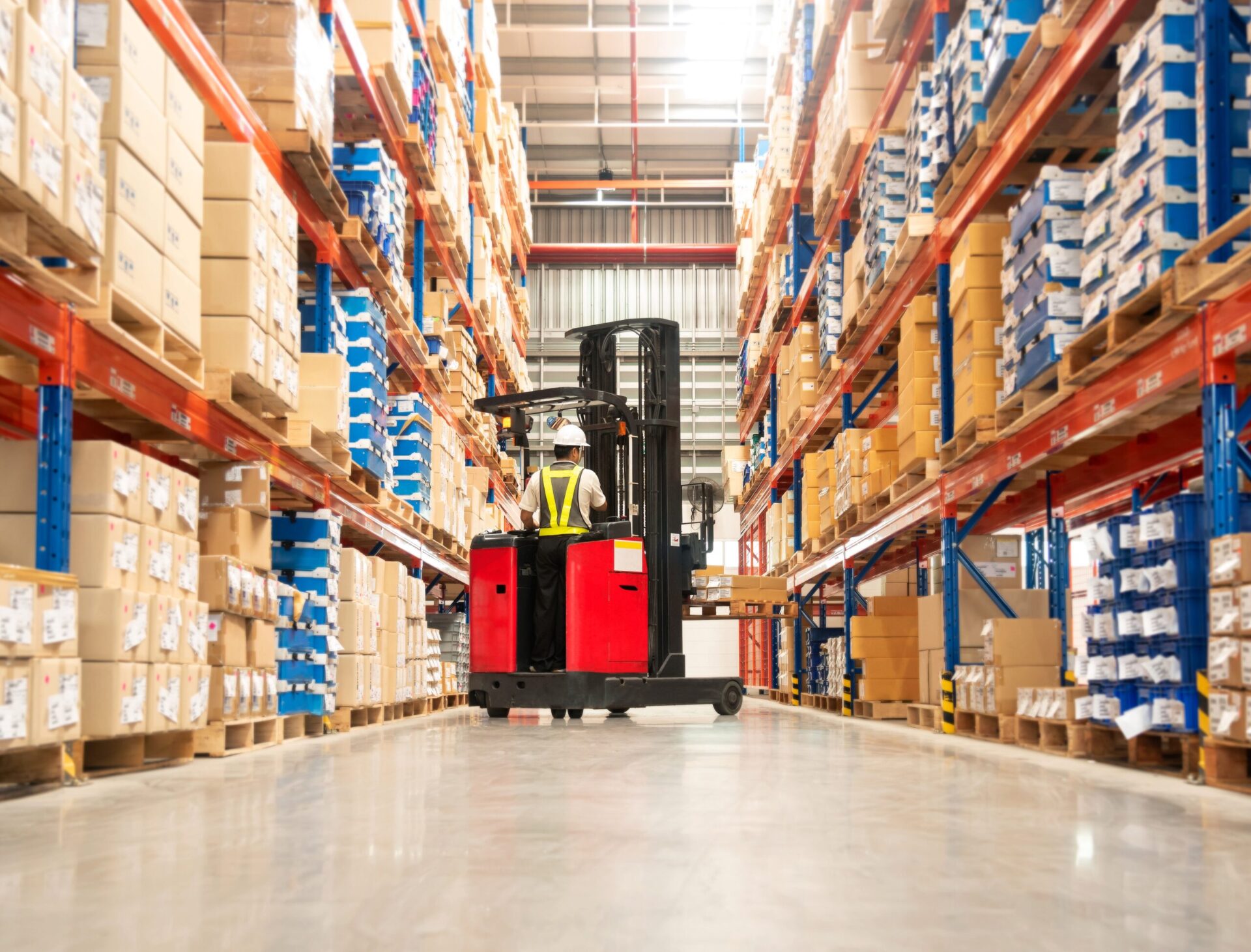
By Charles Fallon
January 25, 2013 | 2 min read
SKU proliferation in food distribution has generally made pick lines longer and reduced the number of picks per foot traveled along the pick line. However, many operations do incur penalties in order selection productivity because of the opposite problem: too many picks per foot traveled creating picker congestion.
To illustrate the problem, picture a foodservice distributor serving a quick-service restaurant chain: the DC supplies 200 restaurants and averages 42,000 cases of frozen product a week from 40 frozen SKUs. To make the situation extra painful, let’s imagine they ship 6 days per week and pick 7 hours per day. That means that every picking hour, the DC needs to pick 42,000 / 6 / 7 = 1,000 frozen cases per hour.
The SKU counts are low and the cases per order line high, so the pickers should be able to manage at least 200 cases per hour. So every hour, the DC needs to put 5 pickers on the frozen pick line. If we double-faced each item, then the pick line would be about 160’ long. That means the average spacing between pickers would be about 32’ – about 4 racks apart.
Is 32’ a large enough spacing to keep traffic moving along fluidly? One way to try and figure that out is to borrow math that transportation planners use to analyze our road network. Unfortunately, that math can make even the most numbers-friendly among us dizzy (if you don’t believe me, start here). Out of that analysis though, we know two basic things:
- There is a minimum spacing needed between vehicles (in our case, pickers) to maintain an acceptable average travel speed
- Below that minimum spacing, small delays upstream can translate into grinding, halting jams downstream
Experience provides a short-cut around the complicated math: the minimum spacing between pickers to avoid picker congestion is somewhere around 50’. When the average distance between pickers falls below that number, productivity will suffer and potentially, suffer mightily. Remember, fork drivers circulate in these aisles too, adding another potential point of congestion.
Back to our example: at first glance, we would conclude that an average spacing of 32’ between pickers is not enough. Those pickers will get jammed and they will not achieve 200 cases per picker-hour. If they cannot hit 200 cases per hour, they need more pickers on the pick line which shrinks the average spacing down even further and picker congestion risks increase even more. It becomes a vicious circle of diminishing productivity.
Reach out to the LIDD team to learn more about warehouse slotting and optimizing your warehouse operations.