Is your Warehouse Layout Up to Date? Receive an Updated Layout in 2 Weeks.
Foodservice WMS Benchmark: Are you maximizing your investment in a WMS?
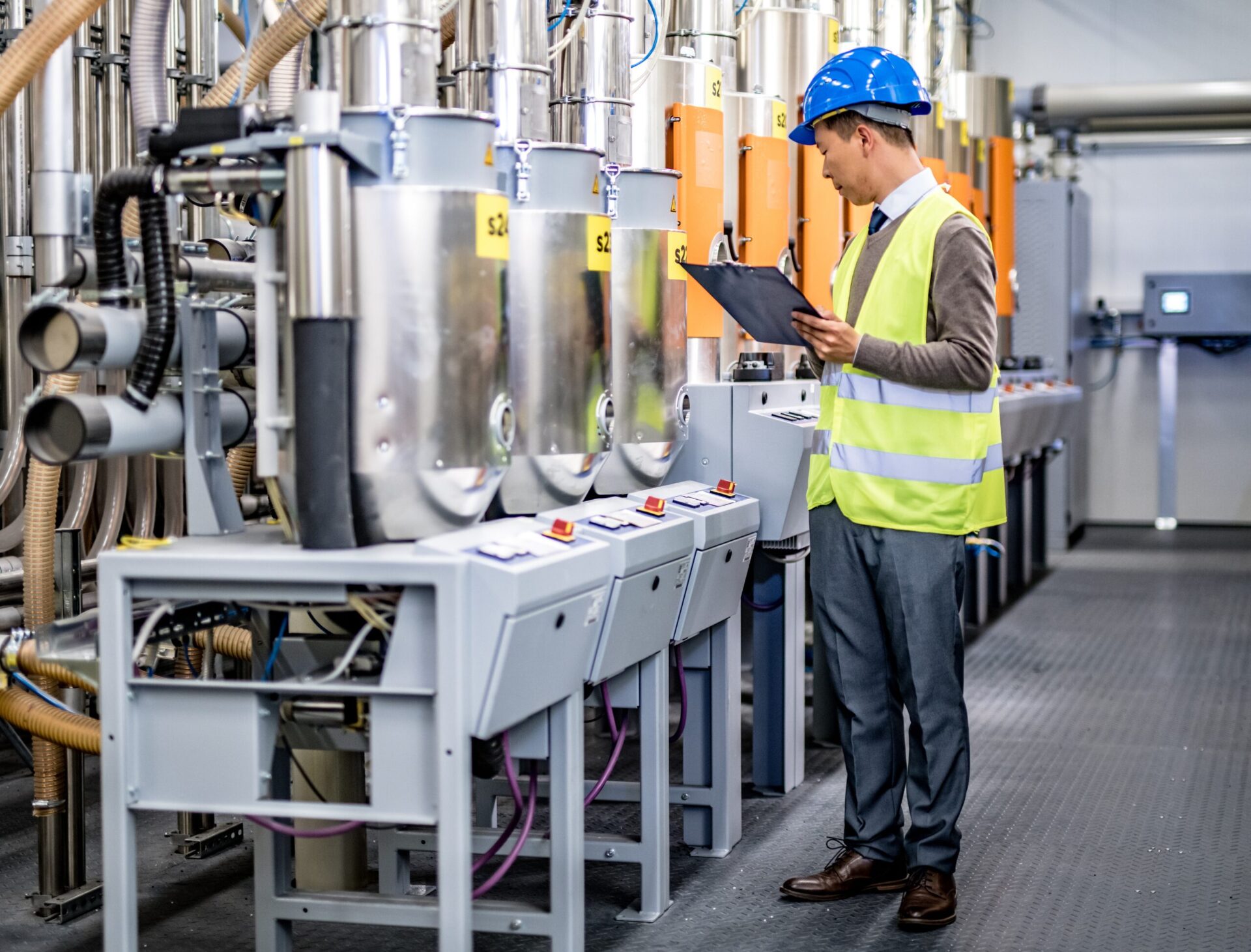
By Jeff Hamilton
August 22, 2017 | 4 min read
The overall performance of a foodservice distribution facility has a strong correlation with the functionality of the software used to run the operation. Splitting companies into two categories according to the functionality in use in their WMS, we see a significant gap in performance:
Activity | Low Performers | Benchmark | High Performers |
WMS Functionality Score | 26% | 44% | 63% |
Cases Shipped per Order Selector Hour | 53 | 85 | 116 |
Cases Shipped per Hour (All Hours) | 27 | 35 | 43 |
Selector Hours as % (All Hours) | 58% | 48% | 37% |
Cases Shipped per Sq.Ft. | 13 | 24 | 35 |
- Facilities with a highly performing WMS are shipping 63 more cases per order selector hour, equivalent to a 120% productivity increase over low performers
- These high performers are 60% more productive per work hour in terms of cases shipped than low performers
- High performers are also using 20% less of their total DC work hours on picking than low performers. They focus more of their efforts on processes that surround picking to generate a more efficient picking process that minimizes disruptions and fills orders at a higher rate.
While our results present a significant evidence that companies should be focused on a highly functional WMS, there is an important caveat; many other factors drive these results, such as: shipping volumes, order profiles, SKU counts, layout, slotting and management.
Bear in mind that DC managers cannot control SKU counts, shipping volumes and order profiles. They can control layouts, slotting and management, and the decisions surrounding them have a salient effect on performance. In combination with serviceable IT infrastructure, these factors are the backbone of any profitable business in the foodservice industry.
Reach out to the LIDD team to learn more about warehouse slotting and optimizing your warehouse operations.