Is your Warehouse Layout Up to Date? Receive an Updated Layout in 2 Weeks.
Navigating Automated Packaging Solutions
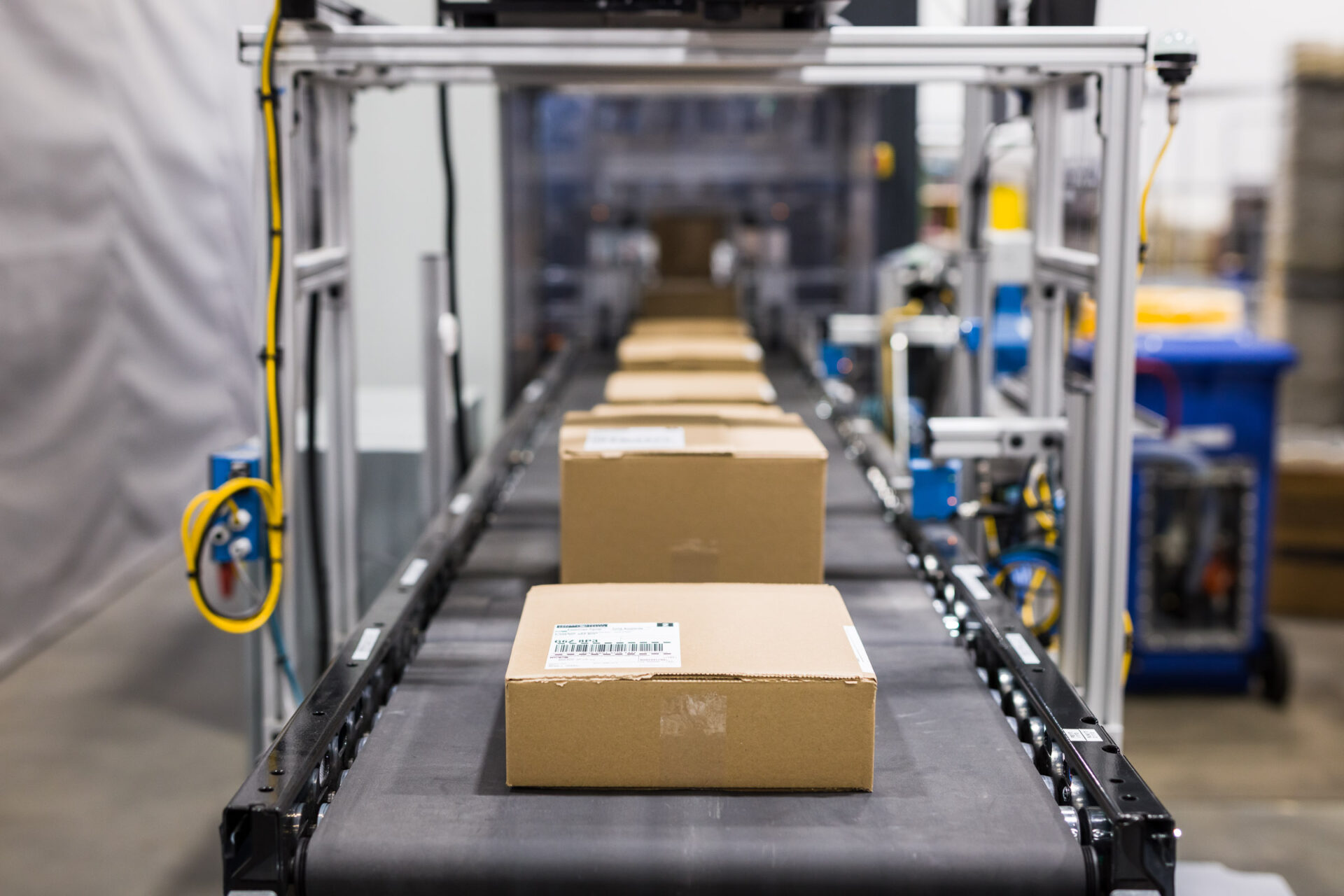
Angie Sabourin
March 13th | 3 min read
Implementing Warehouse Automated Packaging Solutions
Recently, one of our top clients required an automated packaging solution, and the process to make it happen was more involved than it may seem at first glance.
As logistics consultants, we are well acquainted with the complexity of this process, from designing the solution to selecting the technology and making sure everything runs smoothly. But as an outsider, it’s not as straightforward as it might seem.
Here is a glimpse into what’s involved when implementing automated packaging solutions in your warehouse:
Identifying the optimal type of automatic packaging: autobagger, case builder, case erector.
When it comes to what kind of tool best suits your operational needs, there are many options. There’s the autobagger, which deftly handles the task of bagging products; the case builder, which excels in assembling and packing products into cases; and the case erector, which is adept at efficiently forming and sealing corrugated cases.
These advanced systems can handle tasks like erecting boxes, taping cartons, and wrapping pallets for shipment completely on their own, without direct human involvement. This kind of system would be considered automated packing processes that are pre-programmed from start to end. These options are usually good solutions for operations where demand is high or that predict significant growth.
The type of automation solution you need will depend on your products, processes, productivity goals and space in your warehouse.
Finding the right vendor to partner with.
A successful packaging operation begins with a well-planned set-up, and finding the right vendor to partner with is a critical step in the process. This is important because the vendor will supply the packaging materials and equipment that are essential for the operation. By selecting the right vendor, you can ensure access to high-quality products, reliable technical support, timely delivery, and potentially establish a long-term, collaborative relationship.
Working closely with our IT team to validate the necessary requirements for smooth communication with various systems and existing infrastructures (WMS/TMS/ERP).
Any automatic packaging solution needs to integrate effectively with your company’s existing technology landscape. This enables efficient data exchange and synchronization across different operational functions. By validating these requirements early on, potential communication barriers can be identified and addressed, leading to a more streamlined and effective implementation of the automatic packaging solution.
Managing expectations from both the vendor and the customer.
This involves clearly defining and aligning the requirements, capabilities, and deliverables with the vendor to ensure that the automated packaging solution meets the specific needs of the business.
Defining the electrical and pneumatic requirements for machine installation.
An easy step to overlook, but your machinery is nothing without the infrastructure to support its installation and operation. This includes determining power supply requirements, voltage specifications, compressed air supply needs, and any other electrical or pneumatic dependencies necessary for the seamless integration and functioning of the packaging equipment within the facility.
Creating operational flows to ensure packages are delivered automatically at the desired packing time.
Operational flows are designed to ensure that packages are automatically delivered at the desired packing time. This involves mapping out the entire packaging process, including the movement of products from the production line to the packaging station, the activation of the packaging machinery, quality checks, labeling, and the efficient delivery of packaged goods for distribution or storage.
This step is important because it directly impacts the efficiency, accuracy, and timeliness of packaging operations, ultimately influencing the overall productivity and customer satisfaction.
Developing training manuals for machine maintenance.
These manuals are essential for ensuring that maintenance personnel have the necessary knowledge, skills, and procedures to effectively care for and repair equipment. By following these guidelines, the risk of unexpected equipment failures and downtime is reduced, promoting overall equipment reliability and operational continuity.
Assigning responsibility for the machine to the relevant department (maintenance, logistics, IT).
Assigning responsibility for the automated packaging machine to the relevant departments, such as maintenance, logistics, and IT, ensures clear ownership and accountability for different aspects of the machinery’s operation. This step involves delineating roles and responsibilities, establishing communication channels, and coordinating efforts to optimize the performance and reliability of the automated packaging system. Since it’s new operations in a warehouse, sometimes it might fall into the cracks.
Addressing any other questions and concerns that vendors and customers may have.
Exploring and resolving any additional inquiries or issues that vendors and customers may raise is a big aspect of the process of evaluating and implementing automated packaging solutions. While the list I have shared offers a brief glimpse into the multifaceted nature of this endeavor, it’s important to recognize the range of factors and considerations involved. This is where transparent communication and clarification around customer or vendor concerns need to be addressed effectively to better fine tune the solution to meet their exact needs and requirements.
In a nutshell, investing in packaging automation means building the right team to make strategic decisions and putting processes in place to keep your packaging automated system running smoothly.
For us logistics consultants, that’s just business as usual!
For more information about how LIDD’s warehouse technology team can help you maximize the value of your warehouse technology systems – including automated packaging solutions, get in touch with a LIDD expert today.