Is your Warehouse Layout Up to Date? Receive an Updated Layout in 2 Weeks.
Is your Warehouse Layout Up to Date?
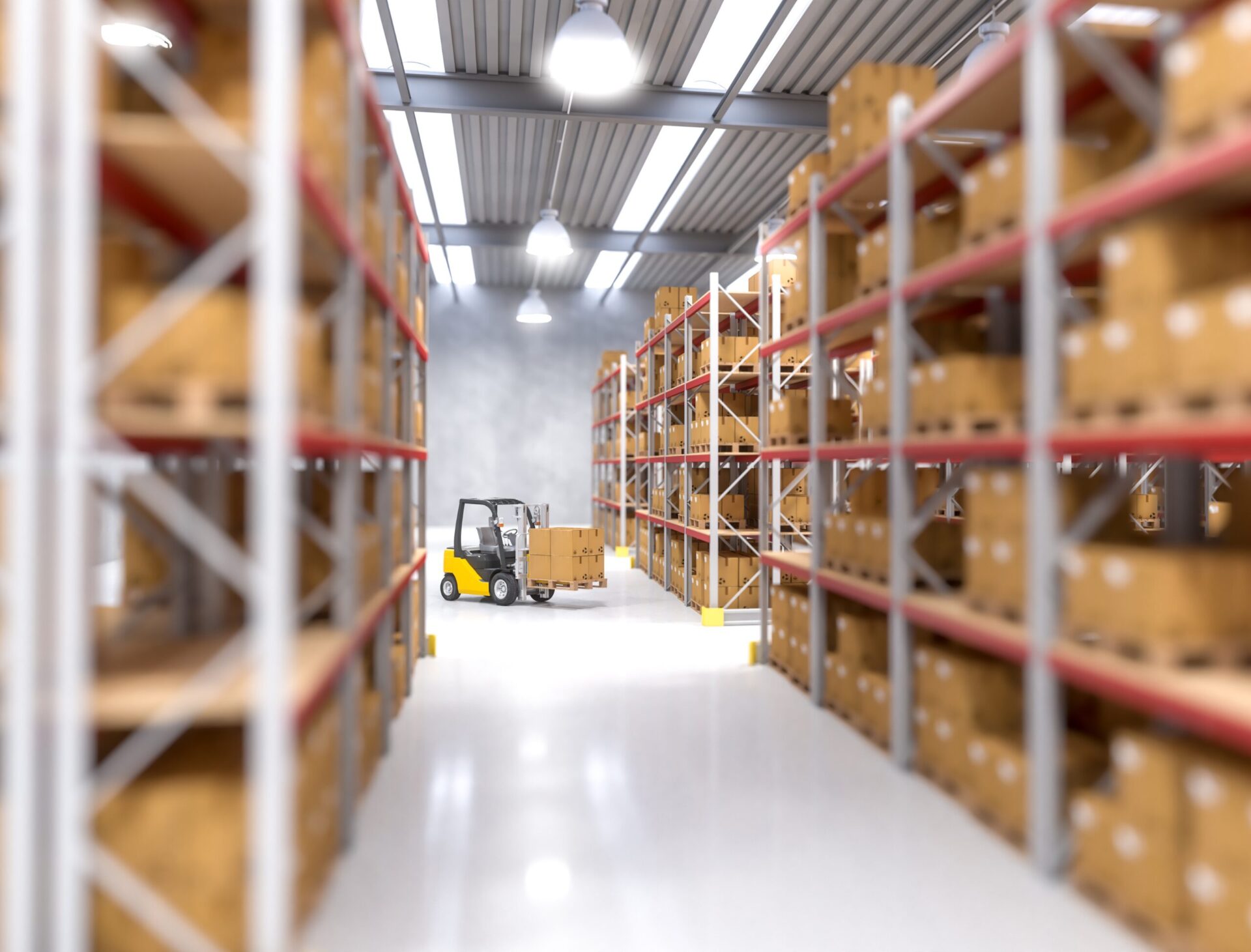
By: Rebecca Granitto
Mar. 3, 2025
Why Warehouse Layout Matters
When starting any warehouse design or optimization project, one thing becomes immediately clear: many companies do not have up-to-date or complete warehouse layouts. This issue isn’t new—very few warehouse operators maintain updated plans, and it’s rare for these layouts to include all the critical details that can significantly enhance warehouse efficiency. While some facilities may have a floor plan, it often lacks essential information, such as rack elevation drawings, building dimensions, and the location of key obstructions. This lack of updated information can lead to operational inefficiencies and missed opportunities for improvement.
For warehouses to run efficiently, a comprehensive layout that reflects current conditions and future needs is crucial. Not only does it allow businesses to plan for expansion, but it also helps optimize workflows, reduce costs, and improve safety. As industries evolve, having a solid warehouse layout is vital for streamlining operations.
The Importance of Accurate Warehouse Design
A complete warehouse layout typically includes:
- Rack and aisle layout: Including all rack dimensions such as upright center-to-center, rack depth, spacer length, and other storage equipment types.
- Aisle widths and clearances: Details on aisle widths and space between racks and walls to ensure smooth operations.
- Rack elevation profiles: Including floor-to-top-of-load-beam measurements for all racks, crucial for understanding storage capacity.
- Pick slot details: Number of pick slots, including hand-stack and flow-rack slots.
- Conveyor layouts: To determine the most efficient flow of materials within the facility.
- Building dimensions: Column sizes, spacing, and clear heights.
- Location of obstructions: Such as sprinkler risers, downspouts, and air units, which can affect storage space.
- Dock and door details: Including the size and location of dock doors, personnel doors, and cooler/freezer doors.
The Physical Audit Process
Conducting an accurate physical audit is a vital step in the process of updating a warehouse layout. The audit typically involves measuring the facility’s key features with tools like a measuring tape and handheld laser devices. While this can be physically demanding, it is necessary for creating precise drawings and models. Larger facilities may require a few days to complete, but even smaller, more complex warehouses can be audited efficiently with the right experience and tools.
Once the layout is accurately recorded, typically in AutoCAD, the next step is to calculate the facility’s cubic storage capacity. The audit also helps familiarize the team with the facility, reducing the risk of errors from missing or incorrect data.
Real-World Application: Foodservice Distribution
Recently, LIDD worked with a large distributor of consumer goods and packaged food to help them update their warehouse layout. This project focused on optimizing operations across their network of facilities in Mississauga and Calgary. Here’s a look at the project steps:
Project Overview:
- LIDD measured all relevant infrastructure at both the Mississauga and Calgary Distribution Centers (DCs).
- We recorded the profile and location of all fixed equipment and documented the warehouse layout in AutoCAD.
- Our team also created capacity models and updated the layouts based on current operations, preparing them for future expansion and efficiency improvements.
- The client requested to review the layout and discussed splitting the capacity into different zones.
Project Steps:
Phase 1: Initial Creation
- Document existing layouts: Using existing facility drawings, LIDD recorded the physical infrastructure of each DC.
- Measure all elements: We measured building features, equipment, and obstructions.
- Record fixed equipment profiles: The location of racks, conveyors, and other fixed assets was documented to ensure accurate modeling.
- Layout capacity calculation: Based on the measurements, LIDD calculated their storage capacity.
Phase 2: Ongoing Maintenance
- LIDD can continue to support the company by regularly updating warehouse layouts and capacity models to reflect any changes. This is especially useful when significant updates are made to the facility or to operations.
Results and Impact
Why was LIDD brought in? The client needed a reliable, up-to-date layout to ensure their warehouses were functioning at peak efficiency. By incorporating modern design principles and an accurate, data-driven layout, LIDD prepared the company to identify opportunities to improve workflows, enhance storage, redesign the layout, and support scalability.
Though results from this project are still being analyzed, the goal was to enable the client’s facilities to better accommodate their growth and adapt to future operational needs. When ready, they will be able to provide their vendors with a layout plan.
Why Should You Update Your Warehouse Layout?
Having an updated warehouse layout not only reduces inefficiencies but also offers the following benefits:
- Optimized space utilization: Maximize available space, allowing for more efficient storage and handling.
- Improved workflows: Streamline processes, from receiving to picking and shipping.
- Cost savings: Eliminate bottlenecks and reduce unnecessary labor costs.
- Future proofing: Set up your facility for future expansion, automation, and changes in inventory flow.
Getting Started
Ready to update your warehouse layout? Our expert team can deliver accurate, updated layouts in just 2 weeks. Contact us today to get started on improving your warehouse efficiency and planning for future growth!
Related Posts
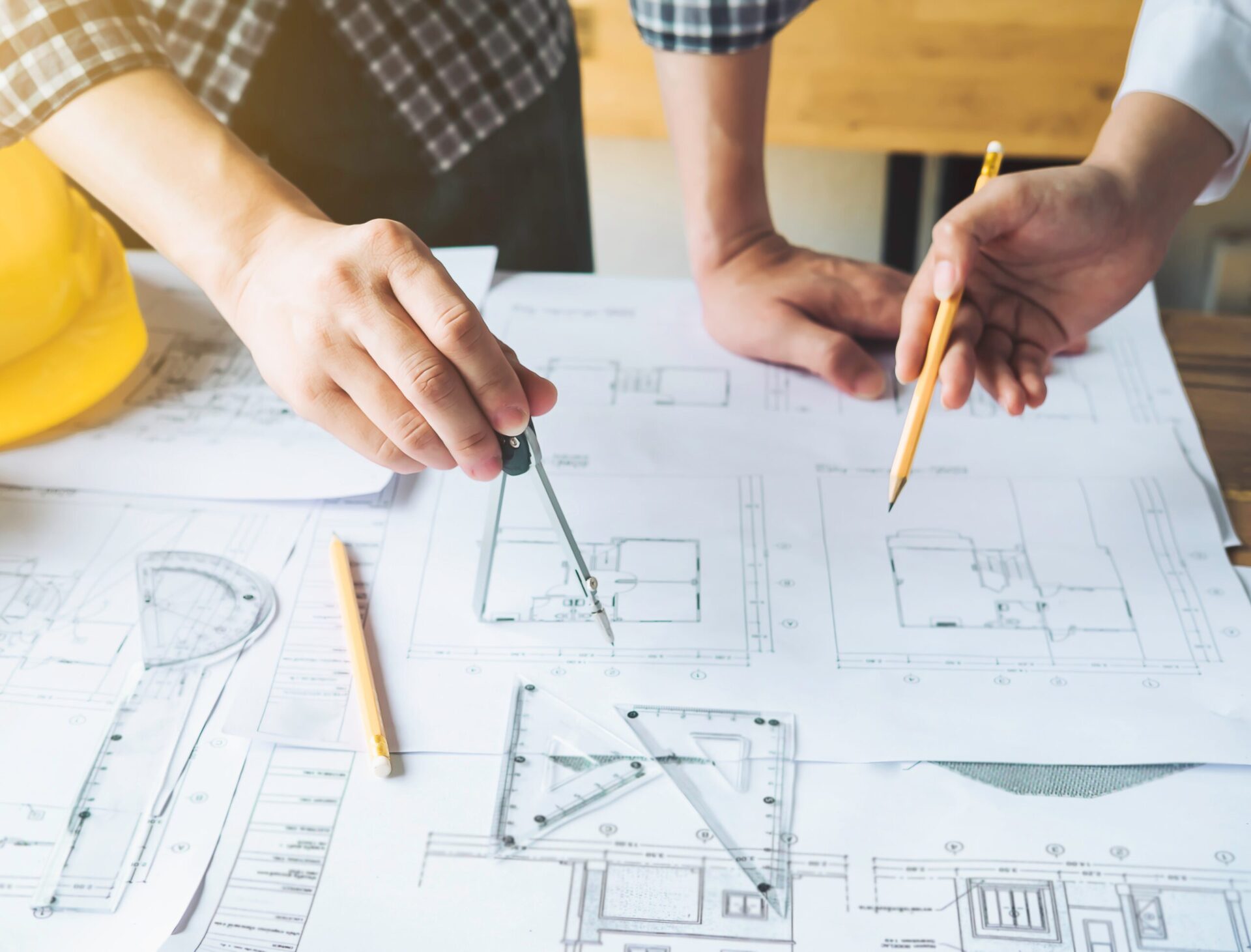
Every Facility Should have an Up-to-date Warehouse Layout
When we start a project, we’re never surprised to find out that the client doesn’t have up-to-date or complete plans of their warehouse. Very few operators have up-to-date warehouse layouts, almost none have all the useful information that can be included on these drawings.
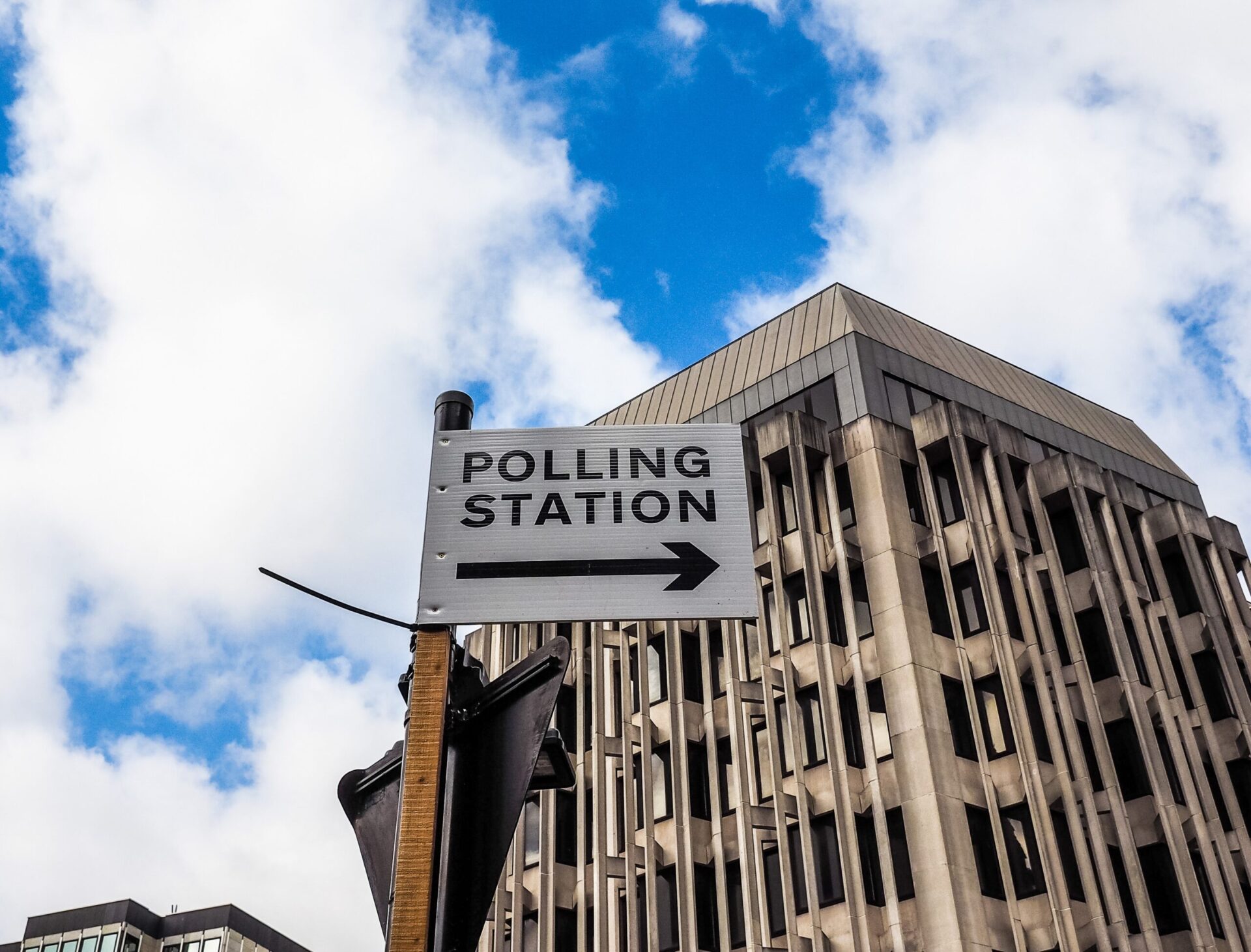
A Warehouse Is Like a Polling Place
By Gabrielle Tiven November 29, 2016 | 2 min read This election season I had a strategy for voting….
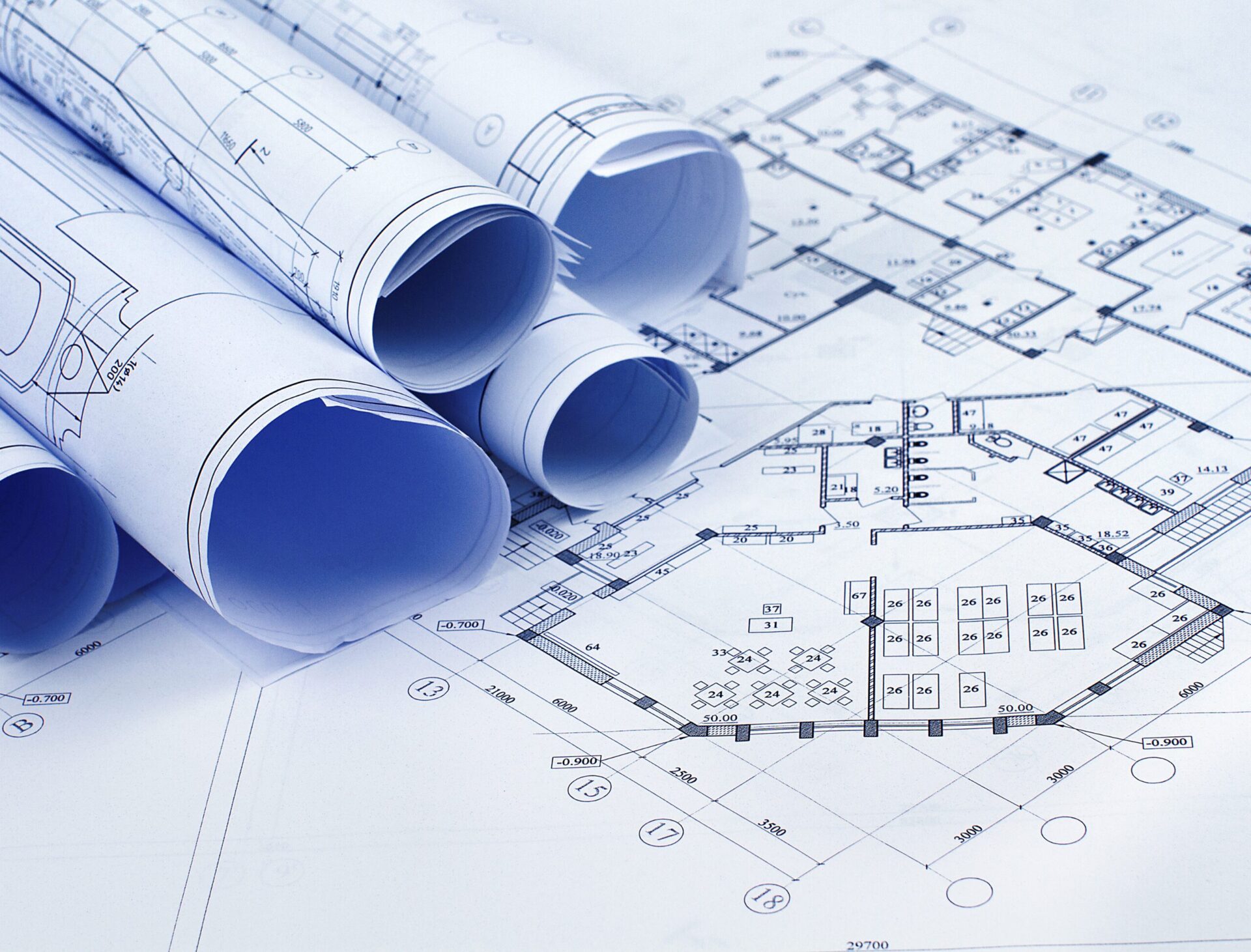
Conserving Capital in a Clever Warehouse Design
LIDD study reveals significant infrastructure investments needed for SAQ to manage glass bottle recycling in Quebec. Learn about the challenges and potential solutions.
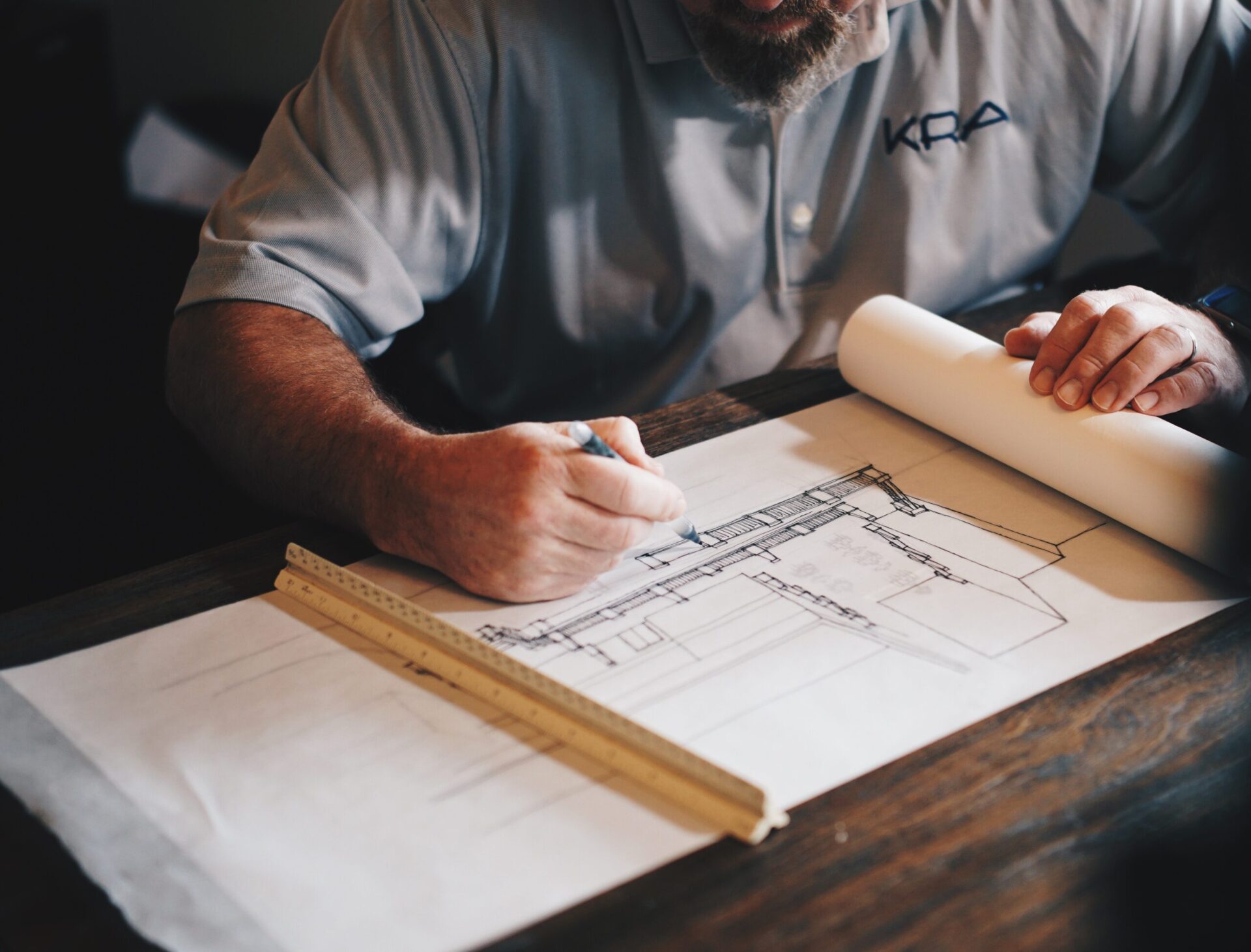
How 3D CAD Modelling is Useful in Warehouse Design
Learn how 3D modeling enhances warehouse layout design. Discover the benefits of using 3D for complex layouts and equipment planning.
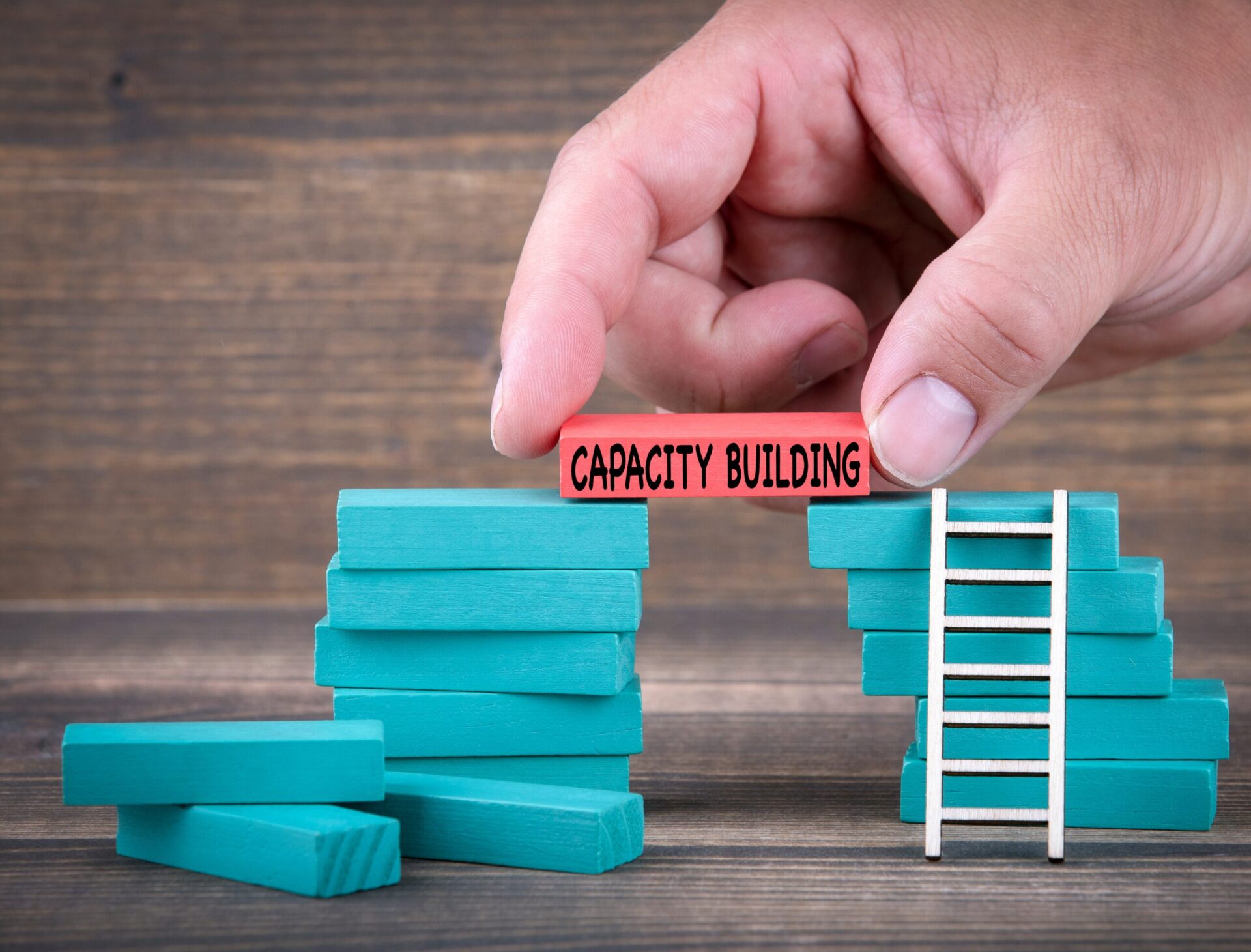
Finding Hidden Warehouse Capacity
By Charles Fallon July 21, 2017 | 2 min read Warehouse storage capacity constraints can arise for a variety…
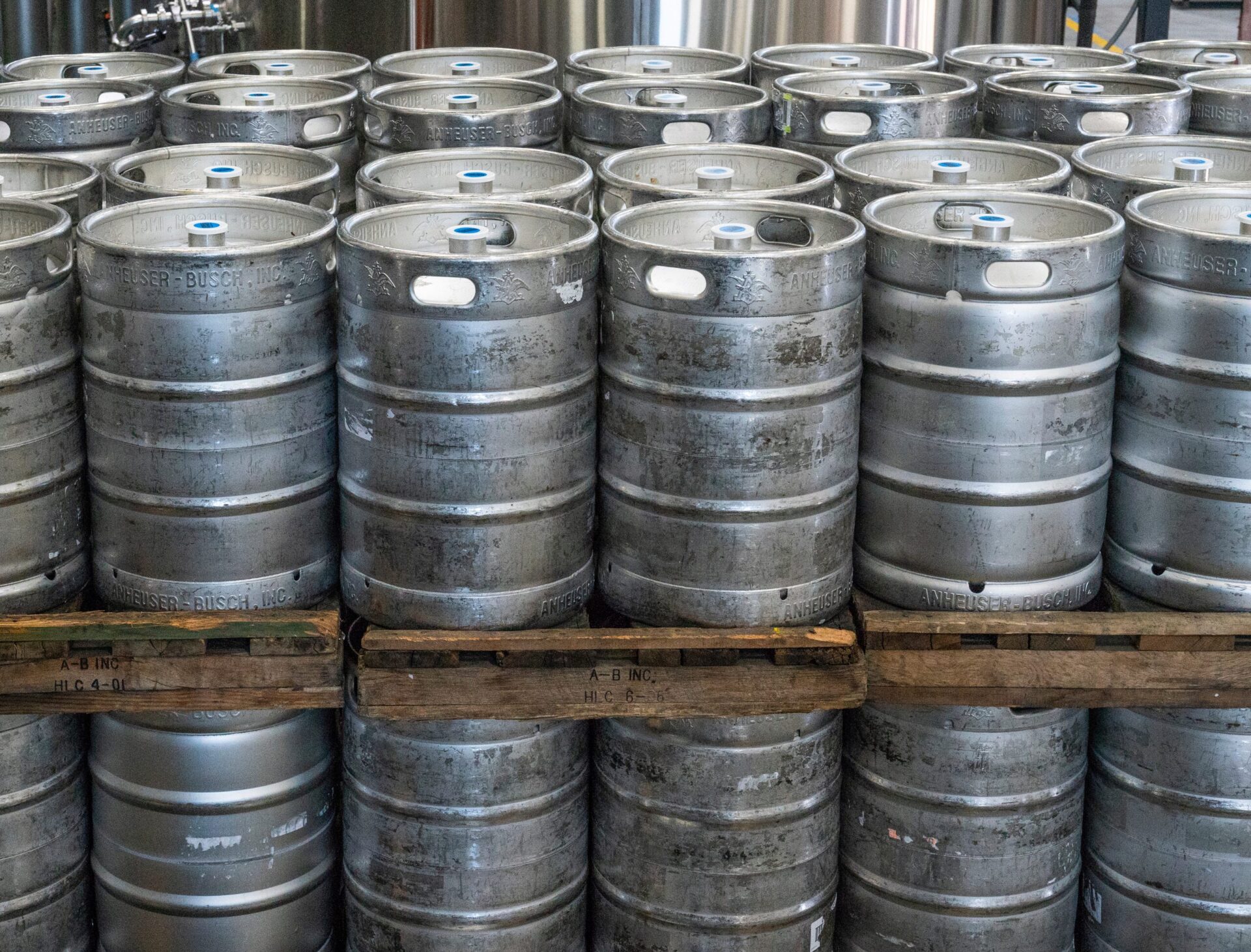
Bulk Storage: Are you using it efficiently?
Learn how to optimize your warehouse layout storage for maximum efficiency. Discover strategies to improve bulk storage utilization and overall warehouse capacity with LIDD’s expert insights.