Is your Warehouse Layout Up to Date? Receive an Updated Layout in 2 Weeks.
Why should I care how my 3PL distribution is run?
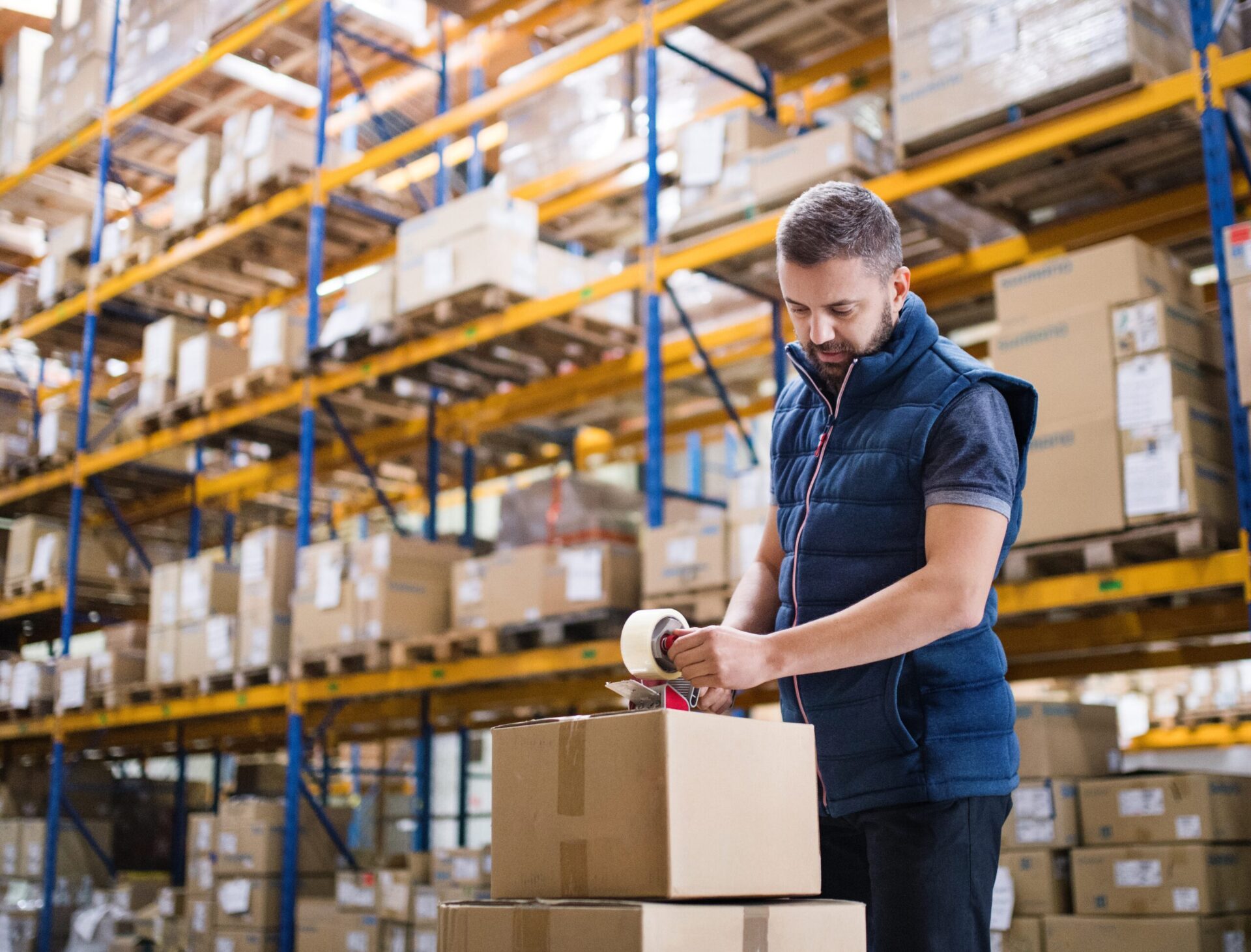
By Charles Fallon
December 12, 2016 | 2 min read
The Director of Logistics at one of our new clients asked me this question recently. She went on to say that since the 3PL charges for pallet movements and pallets stored, how they do their job isn’t really her concern. That is a dangerously expensive position to take if you are a substantial consumer of 3PL services. By substantial, I mean:
- One or a combination of 3PLs execute a big chunk of your distribution (e.g., > 10%)
- That chunk of distribution is large (e.g., > 100,000 sq.ft.)
- You use a 3PL over a sustained period of time (e.g., > 1 year)
How 3PL Distribution Inefficiency Affects Costs
Whatever pricing mechanism is used to calculate monthly 3PL bills, your 3PL can only stay in business if those revenues are larger than the costs to provide your service. A 3PL is no different from any other business – it has to focus on the basic formula that makes it economically sustainable:
Revenues = Cost + Profit
The costs of providing you storage and distribution services will be determined by the nature of your needs and how the 3PL’s infrastructure supports those needs. When your needs and their infrastructure don’t match, there’s a performance inefficiency that adversely affects costs. Inevitably, you will pay for those inefficiencies so that the 3PL protects its profit.
Some examples:
- If you have a low-SKU count, low-turning inventory and the 3PL can only store this volume in selective racking, your product will occupy more square footage than necessary. They will charge you excessive occupancy costs accordingly, regardless of whether it shows up on your bill or not.
- If you have split-case picking operations in a 3PL operation that does not support split-case picking – because it lacks the proper technology, process and/or layout – the picking operation will be less productive than it should be. Again, you will be charged excessive order processing fees accordingly to protect their margins.
Match Your Needs To The Right 3PL Infrastructure
Too often, companies think that handing over distribution to a 3PL means they can just set it and forget it. If shipments go out on time and in good condition and the bills aren’t crazy, then who cares what happens within the four-walls of the warehouse. But that attitude can cost you a lot of money. Over time, those costs will be shocking. LIDD has helped clients save millions of dollars in 3PL costs simply by taking the time to match their needs to the right 3PL infrastructure. And those savings continue when you partner with 3PLs to ensure that their infrastructure evolves with the changing demands of both your businesses.
Are you matching your distribution needs to the warehouse infrastructure of your 3PL? Share your experiences and best practices in the comment box below. I’d love to hear your strategies for lowering storage and distribution costs, while improving your overall supply chain efficiency.
Reach out to the LIDD team to learn more about warehouse slotting and optimizing your warehouse operations.